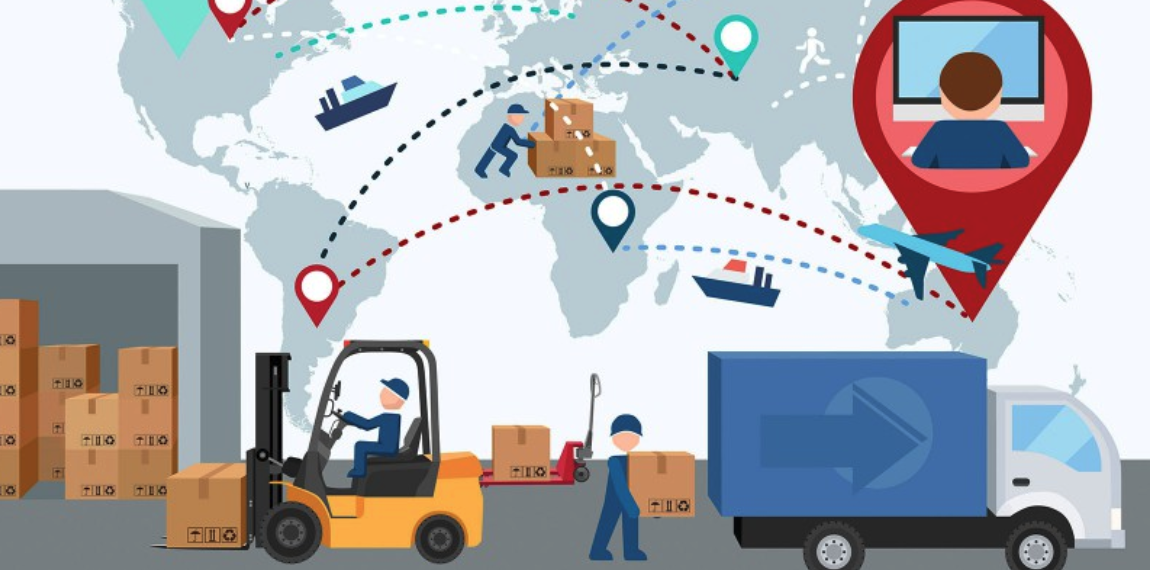
EDI – The order to invoice transaction sets
Dec 15, 2020
The four commonly required transaction sets to support the customer ordering, shipment and billing processes will be covered here. When implemented properly these transactions can significantly improve accuracy and productivity for both trading partners.
EDI 832 price/sales catalog transaction set
Before your customers can submit an order, they need to know what you sell, how much it costs and various logistical characteristics of your products. Before ordering, they must get this information quickly and accurately into their purchasing system. The 832 transaction set supports this. It is effectively your online product catalog that is electronically imported directly into your customer’s system. It includes the following information:
- Product identification number, usually the UPC code
- Product description
- Product pricing
- Terms which can include discounting incentives
- Product logistical information including size, weight, packaging, etc.
EDI 850 transaction set supports purchase orders
It allows customer orders to be directly imported into your system and includes the information you would expect:
- Product
- Price
- Terms
- Packing
- Shipping requirements
Ironically, many smaller suppliers receive these transactions via EDI and then simply print them out and hand enter them because of the expense of acquiring and maintaining integration software. This leaves room for mistakes. Also, as I pointed out in the introduction blog, everyone implements the EDI spec a little differently. Make sure your EDI department, or third-party supplier, maps and provides you all the fields each customer utilizes. Errors can be costly. If your 832 catalog specifies a solid color pack of 6, but Walmart sends you an 850 with an assorted color pack and your EDI implementation doesn’t pick up that specification, you’ve got a huge issue.
EDI 810 transaction set supports electronic invoicing
EDI 810 is a true godsend to billing and AR departments everywhere. The specification includes anything you could want on a good invoice and eliminates the paper generation and handling on both ends. As long as your 810s are timely and accurate, gone are the days of lost invoices and data keying errors.
So far EDI, if properly implemented, in the form of the 832, 850 and 810 transactions sets are win-win propositions with improved accuracy and productivity on both sides. And that’s all some customers may require. However, many companies also demand the 856 transaction set, Advance Ship Notice, also known simply as “ASN”. The name is a little misleading in that if all it consisted of was confirming the shipment of goods, it would be relatively simple. Unfortunately, it is often much more than that, usually requiring a complete manifest of the shipment broken down by intermediate and final destinations with specially barcoded shipment labels on the packaging. If done properly, this transaction set can help you ensure accurate receiving at your customer’s warehouse, which in turn drives quick and full invoice payment. However, depending on your customer’s implementation and requirements, it can be a very difficult transaction set to support both technically and for the warehouse/distribution side of your business. Doing it wrong, opens a huge compliance deduction exposure. I will dedicate the next blog to the 856.